Best Pulse-jet Cleaning system of bag filter dust collector supplier Philippines
Bag filter dust collector supplier Philippines understands the facts that advantage of pulse-jet cleaning compared to shaker or reverse-air baghouses is the reduction in baghouse size (and capital cost) allowed by using less fabric because of higher gas-to-cloth ratios and, in some cases, by not having to build an extra compartment for off-line cleaning. However, the higher gas-to-cloth ratios cause higher pressure drops that increase operating costs. This form of cleaning uses compressed air to force a burst of air down through the bag and expand it violently. As with shaker baghouses, the fabric reaches its extension limit and the dust separates from the bag. Air escaping through the bag carries the separated dust away from the fabric surface. In pulse jets, however, filtering gas flows are opposite in direction when compared with shaker or reverse-air baghouses.
Caged Filters used by bag filter dust collector supplier Philippines
In conventional pulse-jet baghouses, bags are mounted on wire cages to prevent collapse while the dusty gas flows from outside the bag to the inside during filtration. Instead of attaching both ends of the bag to the baghouse structure, the bag and cage assembly generally is attached only at the top. The bottom end of the assembly tends to move in the turbulent gas flow during filtration and may rub other bags, which accelerates wear.
Often, bag filter dust collector supplier Philippines are not compartmented. Bags are cleaned one row at a time when a timer initiates the burst of cleaning air through a quick-opening valve. A pipe across each row of bags carries the compressed air. The pipe has a nozzle above each bag so that cleaning air exits directly into the bag. Some systems direct the air through a short venturi that is intended to entrain additional cleaning air. The pulse opposes and interrupts forward gas flow for only a few tenths of a second. However, the quick resumption of forward flow redeposits most of the dust back on the clean bag or on adjacent bags. This action has the disadvantage of inhibiting dust from dropping into the hopper, but the advantage of quickly reforming the dust cake that provides efficient particle collection.
To increase filter area in the same volume of baghouse, star-shaped and pleated (in cross section) bag/cage configurations have been developed. The bag/cage combination is designed as a unit to be installed similarly to a standard bag and cage unit. Such units can be used as replacements by bag filter dust collector supplier Philippines for standard bags and cages when additional fabric area is needed, or may be used in original designs. Normal pulse cleaning is used, i.e., no special changes to the cleaning equipment are required. Costs for star-shaped bags and cages are about three to three and-a-half times normal bags and cages.
Cartridge Filters used by bag filter dust collector supplier Philippines
Further increases in filter area per unit of baghouse volume are obtained by using finely pleated filter media supported on a wire framework. This cartridge can be mounted vertically as a nearly direct replacement for standard bags and cages in existing baghouses, or mounted horizontally in original designs. When used as a direct replacement for standard bags and cages, retrofit costs for one case are 70 % of the cost of building a new baghouse. Cleaning of early cartridge baghouse designs is by typical pulse equipment using a blow pipe across a row of cartridges. More recent designs use individual air valves for each pair of cartridges.
One type of cartridge contains an inner supporting core surrounded by the pleated filter medium and outer supporting mesh. One end of the cartridge is open, which allows gas passing through the filter from the outside to exit to a clean air plenum. Cleaning air is pulsed through the same open end, but in a reverse direction from the gas being cleaned. The other end of the cartridge is closed by an end cap. The manufacturing process followed by bag filter dust collector supplier Philippines requires strong, rigid joints where the end caps attach to the filter medium and cores. Epoxy or polyurethane plastics are used to seal the medium against the end caps. The cartridge is held tightly in place against a mounting plate surrounding the hole that connects it to the clean air plenum. Horizontal cartridges are typically mounted in tandem with a gasket seal between them. If not properly mounted or if the gasket material is not of high quality, leakage will occur after repeated cleaning pulses.
Filter media for cartridges may be paper, spunbonded monofilament plastics (polyester is predominant), or nonwoven fabrics. Cartridges may be from 6 in. to 14 in. in diameter and 16 in. to 36 in. in length. The filtering surface is from about 25 ft2 to 50 ft2 for cartridges with nonwoven fabrics, about three to four times as much with spun bondeds, and more than six times as much with paper. A typical cartridge of bag filter dust collector supplier Philippines may have 36 ft2 of nonwoven fabric, 153 ft2 of spunbonded fabric, or 225 ft2 of paper. Pleat spacing is important for two reasons: closer spacing increases filter area for a specific cartridge volume, but closer spacing increases the likelihood of dust permanently bridging the bottoms of the pleats and reducing available filtering area. For non-agglomerating dusts of small particle size, (up to a few micrometers) and benign characteristics for paper, the cartridge may have 12 pleats/in. to 16 pleats/in. Nonwovens under more difficult conditions may have 4 pleats/in. to 8 pleats/in. Pleat depth is 1 in. to 3 in. Pleat arrangement and available volume of cleaning air determine the cleanability of the media for a specific dust. An advantage of paper media is their ability to collect particles less than 2.5 µm in diameter with high efficiency. Overall efficiency can be 99.999+ percent for bag filter dust collector supplier Philippines. Nonwoven media may be an order of magnitude less efficient. However, even glass fiber bags in reverse-air baghouses on combustion sources can collect 2.5 µm particles with 99.9 percent efficiency.
Cartridge filters are limited in temperature by the adhesives that seal the media to the end caps. Operating temperatures of 200 deg F are common, with temperature capability to 350 deg F soon to be marketed.
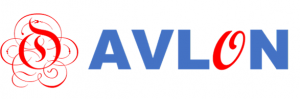