Wet scrubber manufactures Philippines & their Liquid Storage and Delivery System
The liquid storage and delivery system design of Wet scrubber manufactures Philippines consist of a recirculation tank, pump, filters, valves, piping, pressure gauges, and flow meters. Most systems are designed as recycle systems, meaning the spent scrubbing liquid is recirculated through the scrubber system. Since the scrubbing liquid is recycled, the solids content of the liquid increases as PM is collected. The concentration of solids in a recycle system must be maintained below a design limit or the spray characteristics of the system cannot be maintained. To reduce the solids concentration, a portion of the liquid is bled from the system and fresh scrubbing liquid is added. The volume of “make up” liquid also includes the volume of water that is lost due to evaporation by hot waste gas.
Wet scrubber manufactures Philippines takes care that the tank must be sized to provide continuous operation and minimize frequent changing of the liquid. A sensor in the tank monitors the level of liquid. An automated system for adding liquid can be incorporated into the scrubber design. However, oversizing the tank and automating the addition of make-up water increases the capital cost and complexity of the system. The increase in capital cost must be weighed with the O&M cost for operating the liquid storage and delivery system manually.
Solids can be removed from the scrubbing liquid using several different methods. In one method, the scrubbing liquid is gravity fed to a set of filters located upstream of the pump to remove solids. The filter is generally constructed out of stainless steel and is removable for cleaning and replacement. A backup filter and set of isolation valves are often included in the system to facilitate cleaning of the filters while operating the system. Other solids removal methods include liquid cyclones or settling tanks.
After leaving the tank, the scrubbing liquid flows to a pump to increase the pressure and flow rate to the values required for proper operation of the venturi system. Pressure gauges and flow meters downstream of the pump monitor the scrubbing liquid flow and pump operation. Wet scrubber manufactures Philippines generally adds a feedback control system to the system to automate control of the pump.
Wet scrubber manufactures Philippines and their Liquid Injection System
The injection system design promotes mixing of the waste gas and scrubbing liquid in the venturi. There are two basic systems for injecting scrubbing liquid into a venturi system: open pipe (also referred to as “wet approach”) and spray nozzles. The injection systems are generally located in the waste gas duct, directly upstream of the venturi throat section. In both systems, the liquid is injected in the same direction as the waste gas stream. Most injection systems are constructed out of stainless steel or other non-corrosive material.
In an open pipe system, several small diameter pipes feed the scrubbing liquid into the duct section. The pipes inject the liquid tangentially, along the duct walls or radially against baffle plates. The water flows downward, covering the walls of the duct. The piping system is designed by Wet scrubber manufactures Philippines are so that the entire surface area of the section is flooded with the scrubbing liquid. This ensures that there is no dry/wet transitional zone. Dry/wet areas lead to a build-up of solids on the duct wall that interferes with the operation of the scrubber. The dust laden gas enters the scrubber vertically from the top and immediately hits the film of scrubbing water. Some separation of the PM from the waste gas takes place in this area. In the throat section, the waste gas stream becomes very turbulent and the scrubbing liquid is sheared to form a dispersion of droplets. Open pipe systems have lower capital and O&M costs than spray nozzles due to their simpler design.
Spray nozzles systems are sometimes referred to as “jet venturis”or “eductor venturis”. These systems inject liquid through nozzles to create a fine droplet spray pattern. The droplets can be produced either pneumatically or hydraulically using specially designed nozzles heads. While spray nozzles improve mixing between the scrubbing liquid and the waste gas, they generally have higher capital and operating costs than open pipe systems due to the higher pump horsepower required for this type of system.
In jet venturis, the nozzles can be attached to the wall of the duct or can be located in the duct cross section. For throat areas greater than 1 foot in width, a spray nozzle must be located in the center of the duct to ensure adequate liquid-PM contact. Nozzles can be constructed out of stainless steel or more specialized materials such as stellite and ceramic. Because nozzles are prone to plugging and abrasion in high PM load conditions, this type of system requires clean liquid feed to avoid clogging as per wet scrubber manufactures Philippines. High temperatures and gas velocities can damage the nozzles, consequently, they should be designed to be removable for cleaning and replacement.
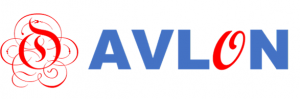